Perhaps this is a bit over the top as far as modeling is concerned as slotting can be done in the lathe or shaping machine! SORRY, I JUST COULDN`T HELP MYSELF, IT`S A 'ONCE A YEAR' MACHINE ALL THE PARTS ARE JUST STACKED ON THE SWARF TRAY AWAITING ATTENTION AND A BRIEF EXAMINATION OF THEM SHOW THAT IT IS A REASONABLE QUALITY MACHINE. – A machine operation in which a work part is fed past a rotating cylindrical tool with multiple edges. (milling machine). Types – Peripheral milling. Slab, slotting, side and straddle milling. Up Milling (Conventional) & down milling (Climb) – Facing milling. Conventional face, Partial face, End, Profile, Pocket & contour.
HomeMachine Tool ArchiveMachine-tools Sale & Wanted
lathes.co.uk
Ajax AJ23 Universal Lathe Attachment
Milling, Grinding and Slotting
Probably unique in that it was equipped with accessories that allowed it to perform four discreet functions - milling, internal grinding, external grinding and slotting - the Ajax AJ23 'Universal Lathe Attachment' was first offered during the 1950s and 1960s when the Ajax Machine-Tool Company was still based in their original Westmount Works in Halifax, Yorkshire, England.
Arranged rather like the amateur-use Potts milling attachment, with a round, vertical column up and down which the various heads could be moved by a screw fitted with a micrometer dial, the Ajax was a much more massive device standing some 21 inches high, around 14 inches wide and intended for use on lathes with a minimum centre height of around 5 inches. A 1/2 h.p. 1425 r.p.m. motor - complete with a no-volt release starter - was an integral part of the unit and could be fitted with different pulleys according to the task at hand.
Three different heads were available: when set up for milling, slotting and external grinding with larger cutters and grinding wheels fitted, the milling head Type B and its motor were each fitted with a 4-step V-pulley, connected by a 37-inch long belt, that gave four speeds of 45, 70, 110 and 190 r.p.m. - these being the recommended ones when using the 2-inch stroke slotting head, the rate being one double stroke per revolution of the spindle. When faster speeds were needed - 90, 140, 220 and 380 r.p.m. - the milling head type B was fitted, it's intended use being with cutters such as side-and face-types on horizontal work. A special high-speed grinding head was also included, this being used for both internal and external work - the latter with a 2-step V-pulley on the wheel arbor that gave speeds of 3100 and 5000 r.p.m. When used for internal grinding (where very small wheels and high speeds are necessary) the drive system was changed for a narrow, 2-step flat type fitted an endless woven cotton belt. The maximum wheel diameter for internal work was recommended to be no more than 2 inches, the slower spindle speed provided for this size being 8000 r.p.m. (to give a surface speed of 4200 feet/minute) and for smaller cutters a higher of 11,000 r.p.m. - the surface speed for a 1-inch wheel then being 2900 feet/minute.
As the head could be tilted over through a maximum inclination was 10° either side of horizontal it was also possible to use the unit to perform worm thread grinding and, to a limited extent depending upon the holding arrangements available, to sharpen lathe cutting tools.
Supplied un-drilled, the 7-inch square base allowed the customer to adapt the unit to mount in a variety of positions: on the saddle, cross slide, top slide or even on some sort of specially modified angle plate or other fitting.
While a number of 'universal' lathe attachments have been marketed with a wide enough range of speeds to allow both milling and grinding to be carried out - a fine example being that by Carstens and others including Cowells and Potts - non so far discovered have managed to combine the four functions of the Ajax AJ23. However, the only accessory offered to make the machine even more useful by mounting very small end mills and slot drills, was a simple blank arbor - at £4 : 2s : 6d each - a number being required as each had to be drilled out to hold a particular size of cutter.
By the late 1950s the unit could be had in several forms: complete with motor and switchgear and both milling and grinding heads at £165 : 0s :0d or with a head just for external grinding at £75 : 0s : 0d or for milling only at £106 : 0s : 0d. The slotting head was an extra £41 : 0s :0d), the pulley kit and two wheel-holding arbors for high-speed internal grinding £17 : 0s : 0d..
Abstract
Our project have the following objectives
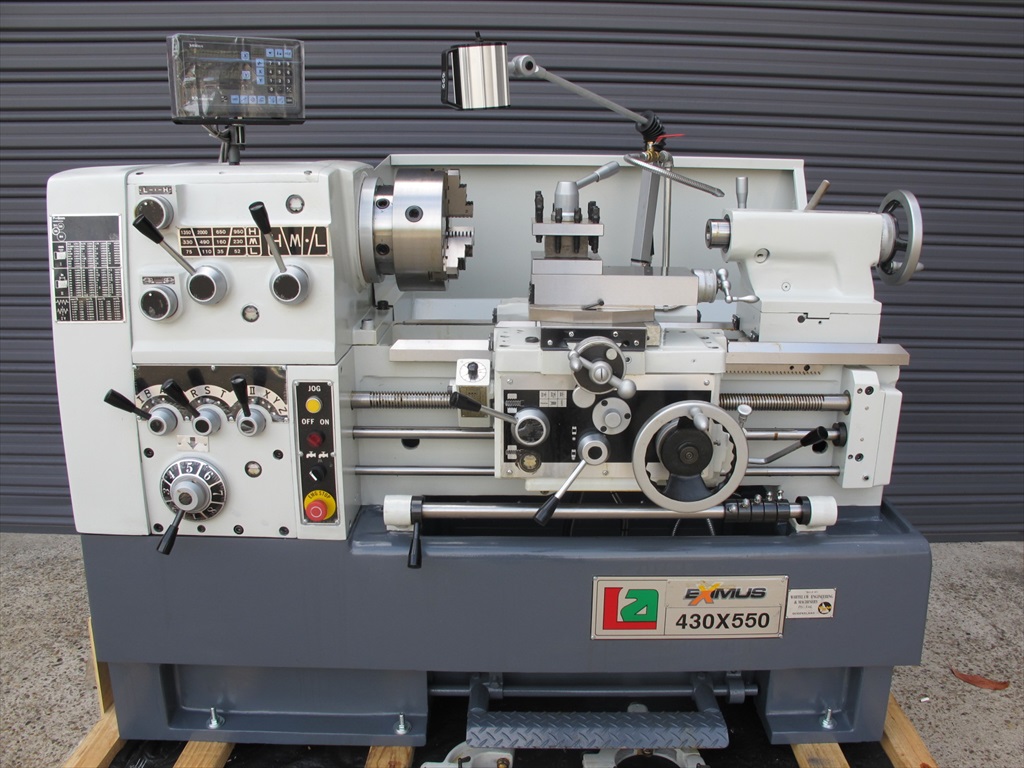